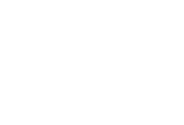
ART CONSERVATOR
DIGITAL
A PUBLICATION OF THE WILLIAMSTOWN + ATLANTA ART CONSERVATION CENTER
VOLUME 17 NO.1 SPLENDOR IN EMERALD: Conservation of an 18th CenturY chair from the Briati workshop
CHRISTINE PUZA | DEPARTMENT HEAD OF WOODEN OBJECTS + FURNITURE
This magnificent 18th century Italian chair is a recent important acquisition by the Corning Museum of Glass (figs.1-2). It has been in private hands for over 250 years and, until now, has never been publicly exhibited. It was made in the workshop of Giuseppe Briati, one of the most notable and successful glassmakers of this time period.
In 1686, Briati was born on the island of Murano to a long-established glassmaking family. The family’s name was registered in the so-called Golden Book (Libro d’Oro) (fig.3) by the Venetian Council of Ten, titled as “Cittadini di Murano”. Once approved and registered in this way, listed families could use the official title of “glass producers and glass makers” and were treated like nobility. This title allowed them to perform public duties, take part in Council matters, and permitted them to make metal coin medallions called “oselle” emblazoned with their own crest and name.
COMBINING GLASS MAKING TRADITIONS
FIGURE 3. The Libro d'Oro or "Golden Book" used to register glass producers and makers during eighteenth century Venice.
“Crystal” glass produced with chalk and potash is stronger, more stable, and exhibits greater brilliance and clarity when compared with the traditional Venetian soda-ash glass in production at the time. Bohemian potassium lime glass also has working properties that allows for the formation of more elaborate structural forms. It also lends itself well to intricate surface decoration, using the techniques of wheel cutting and reverse etching (fig.4).
FIGURE 4. An example of Bohemian glass. Maker: Circle of Dionysio Miseroni (Bohemian, Prague 1607-1661 Vienna). Two-handled glass cup. Mid-seventeenth century. Metropolitan Museum of Art.
Returning to Murano with his newfound knowledge and expertise, in 1737, Briati obtained a ten-year privilege from the Council of Ten to produce glass according to Bohemian methods. In 1739, he used his business savvy to negotiate exclusive access to a source of potash for his workshops, which allowed him to produce glass closer to Bohemian glass formulas. Due to this special arrangement, he was able to sell his wares for prices that undercut his Bohemian competitors as well as his Venetian countrymen.
Seeking to further distinguish himself, Briati quickly developed his own signature style, spurning the traditional Muranese style of colorless blown vessels for raucous colors. He also used an array of glassmaking techniques in his work, such as the use of applied cast glass elements and hot worked elements and inlay. Never satisfied with the ordinary, he continued to push the limits of technical mastery in glassmaking, going on to produce large scale glass objects such as chandeliers, mirrors, and furniture (figs. 5-6). He was so successful in his endeavors that the Venetian government granted him a larger quota of workers as well as access to disability funds to support those who became injured.
FIGURE 5. Dessert Decoration in the form of a Glass Garden. Maker: Briati, Giuseppe Lorenzo (Italian, 1686-1772). Opaque white, opalescent colorless and opaque colored glass; lampworked, assembled, glued. c.1760. Corning Museum of Glass.
FIGURE 6. Chandelier. Maker: Briati, Giuseppe Lorenzo (Italian, 1686-1772). Opaque white, opalescent colorless and opaque colored glass; lampworked, assembled, glued. c.1730. Museo del Settecento Veneziano, Ca' Rezzonico, Venice. Image credit: Venezia Autentica.
However, that same year that he received these honors, his furnace was attacked by an angry group of Muranese glassmakers, who led a night assault on his workshop with firearms. This attack compelled Briati to apply for and receive yet another special dispensation: he was allowed to relocate his workshop to Venice, away from the island of Murano and his detractors, where he continued his incredible success. His fame grew and his products were proclaimed, in the forms of “arm chairs, frames, fruit, flowers, statues, and a thousand other ingenious works […] had now become, “the delight of all the cultured nations” [1].
OBJECTS FIT FOR ROYALTY
Briati’s works had international interest and acclaim. On November 23, 1756, the aristocratic traveler and writer, Lady Mary Wortley Montagu (1680-1762), wrote from Padua to her daughter, regarding a short trip to Venice. Writing of the Venetian glasshouses, Montagu reported she was shown:
“a set of furniture, in a taste entirely new; it consists of eight large armed-chairs, the same number of sconces, a table and prodigious looking-glass, all of glass, it is impossible to imagine their beauty; they deserve being placed in a prince's dressing room, or grand cabinet; the price demanded is 400 £. They would be a very proper decoration for the apartment of a prince so young and beautiful as ours” [2].
The “prince” in question would be the future George III. The price of £400 equates roughly to $170,000 today. For comparison, A middle-class family in England, comprising five members and two servants, would have an annual income of about £200. A glassworker in England earned around £12 in a year. An intricately made object like the Briati Chair would be out of reach for the vast majority of the population, only attainable for the most elite and royal markets of Europe. From Montagu’s description, we might be able to extrapolate that Briati’s furniture was sold in complete matched sets, a common practice of the high-end furniture ateliers of the time. At the very least, chairs could have been sold in pairs and clearly provided rest for an exceptionally important figure who could afford such luxury.
With regards to its provenance, this chair has been privately owned for over 200 years by a Spanish noble family; there is an as-yet unverified possibility that it may have formed part of the diplomatic gift presented by the Venetian Republic to Princess Isabella of Parma (fig.7) on the occasion of her marriage to Joseph II of Austria in 1759.
FIGURE 7. Jean-Marc Nattier, Princess Maria Isabella of Parma, 1758, oil on canvas, Kunsthistorisches Museum Wien, inv. GG 2069.. .
PRESERVING HISTORY | CONSERVING THE BRIATI CHAIR
Despite its age, the chair (fig. 8) was in generally good condition when it arrived at the Center. It features several different types of inlaid glass ornament. Molded rosette medallions and acanthus scrolls decorate the perimeter of the seat (fig.9); C-scrolls of hot worked glass decorate the sides of each leg (fig.10). There are scalloped aprons on the front and sides, inset with cabochons (polished gemstones) and molded shells (fig.11). Large pieces of hot-worked glass are inset into the arms and along the legs, highlighting the undulating lines of the chair (fig.12).
The crest rail is also ornamented with cabochons of several sizes and shapes and molded glass shells with a central mirrored reverse-cut panel depicting a group of three putti (fig.13). Rows of cabochons run along either side, as well as along the perimeter of the seat. The seat is also decorated with a row of small faceted glass jewels. The wood surfaces of the chair are gessoed and watergilded, with an orange-red bole visible in worn areas. Some looseness was noted in the joinery in the left armrest, but the other joins remain tight.
There is minor variation in the green color of the glass ornament; they are mostly a medium emerald green, but some are lighter and more turquoise in color. X-ray Fluorescence (XRF) with a Niton XL3t XRF Analyzer was used to investigate the composition of the glass. There was a major peak for Lead, followed by Iron and Copper, with minor peaks for Potassium and Calcium. In this case Iron and Copper provides the green color to the glass; in modern green glass chromium can be found. Both the dark green and the brighter turquoise green glass elements had similar spectral compositions, varying only in proportions of Iron and Copper.
The wood surfaces of the chair are gessoed and watergilded, with an orange-red bole visible in worn areas. Some looseness was noted in the joinery in the left armrest, but the other joins remain tight. As with most European objects of any age, the chair has undergone numerous rounds of restoration and repair. Areas of loss to the gilded surfaces have been previously filled and inpainted and/or gilded with varying degrees of skill. There are also many different campaigns of replacements of missing glass ornament.
In some of these, insets of carved and shaped wood have been applied as compensation for lost ornament; these have been painted with a glossy dark green paint. These types of replacements are mostly seen in areas of missing cast ornament, but there are a few examples of missing cabochons being compensated for in this way. The other method of missing ornament replacement has been made from a hard green plastic, which has been molded into the shape of the missing cabochons.
The largest and most glaring loss to the glass ornament is to the curved inlay on the right front leg, where a 4” section of glass is missing (fig.14). This loss appears to have been caused by a significant impact; there is considerable gesso loss around the missing section of glass and some tearout and loss to the wood beneath. The glass above and below the loss also appears to have some internal fractures.
FIGURE 14. Detail of loss glass ornament along the front right leg
Visible in the cavity there are remnants of a silver foil that appears to have been applied as a backing material before the glass ornament was adhered in place. The silvering on the crest rail mirror is blotchy and discolored, with detaching flakes. It is captured inside of a compartment that has been sealed from the back and secured with fine nails.
The chair arrived missing its back upholstery. The seat, however, was upholstered with an overstuffed cushion with a steel coil spring core and a show cover comprised of a taupe cotton twill with edge piping and green banding. The high profile of the seat not only was inappropriate for this time period, but also partially obscured the cast glass ornament around the seat. This could not represent the original upholstery scheme, as the use of steel coil springs in upholstery dates to the mid 19th century at the earliest. Given this, all of the unoriginal upholstery was removed, revealing four layers of alternating strata comprised of vegetable material, jute cloth, polyester fill, and muslin over the tied spring core (fig. 15). Three layers of fabric were nailed to the bottom of the seat, representing several different applications of dust covers.
FIGURE 15. Detail of materials uncovered after removing unoriginal upholstery
All of the glass surfaces on the chair appeared dull overall, covered with a milky grey film. The film was tough and only partially soluble in xylene. FT-IR analysis performed in our analytical lab at the Center showed that it was a layer of Rhoplex™ (an acrylic adhesive) that had been applied over all the glass components as a consolidant. Despite its solubility in xylene, the most effective removal of this coating was mechanical, achieved with a scalpel or a swab stick wrapped with superfine steel wool. Though painstaking, this revealed the hard shine of the glass ornament and restored its brilliance, particularly in the faceted jewels.
The loose joinery in the arm of the chair was secured with high tack fish glue. Cracked and flaking areas of gesso were consolidated with Lascaux medium for Consolidation, which was wicked into cracks and under areas of lifting gesso. Loose glass ornament was secured with Paraloid B-72 in acetone. Small losses were filled with Aquazol® based gesso bulked with calcium carbonate or Flügger®, then inpainted with Golden® acrylics. Missing glass ornaments, including the large loss at the right front leg were cast in Epo-tek® (an epoxy resin) using molds taken from the original ornament. The resins were tinted with Orasol® dyes to achieve a suitable color and translucency. Golden® Porcelain Restoration glaze was used as a final surface coating on the cast replacements to achieve the hard shine that mimics the surface quality of the other glass components.
cONCLUSION
The final results of treatment are an object that is structurally secure and visually harmonious (fig. 19-20). The removal of the jarring unoriginal upholstery and minimization of previous treatments allows the object itself to be interpreted without distracting campaigns of previous restoration. Once treatment is completed and the chair arrives at its new home at the Corning Museum of Glass, this magnificent and unique object will be ready to make its grand debut.
ACKNOWLEDGEMENT
With thanks and appreciation to Dr. Christopher Maxwell (former Curator of Early Modern Glass at the Corning Museum of Glass and currently Samuel and M. Patricia Grober Curator, Applied Arts of Europe at the Art Institute of Chicago), for sharing his research and acquisition notes on the historical context of the Briati chair.
Photography Credit | Matt Hamilton, Christine Puza, & Maggie Barkovic
REFERENCES
[1] G. F. Zanetti, Della origine di alcune arti principali appresso i Veneziani, Venice, 1758, p. 83.
[2] Museo del Vetro, Venice. Rosa Barovier Menatasti and Cristina Tonini, Fragile. Murano: chefs d’oeuvre de verre de la Renaissance au XXIe siècle (Musée Maillol, Paris: 2013 .
[3] In Sparkling Company: Reflections on Glass in the Eighteenth-Century British World (The Corning Museum of Glass: 2020): pp.30-33, 204-205.
[4] Robert J. Charleston, Masterpieces of Glass: A World History from The Corning Museum of Glass, New York: Harry N. Abrams Inc., 1980, p. 179.